A CBRN system delivery project is established when there is need to manage a customer specific system, which includes project services. Arto Penttinen described recently in his blog what is required for a successful Naval Project. I would state that the same principles will apply to any CBRN project; from bomb shelters to government facilities or other public buildings, such as airports or railway stations, from naval vessels to land vehicles, you name it. In the next paragraphs is described a typical project life span step by step.
Step 1
Order Review
From the project manager’s point of view a CBRN project starts when the internal order review meeting is held, and that is done as soon as possible after receiving customer PO. All internal stakeholders are usually present: procurement, sales, engineering, production, projects, logistics etc. ODR equals project charter where sponsor gathers all necessary and available information from sales so that the project manager could proceed to start project activities. In ODR meeting the initial scope of delivery and schedule are defined, as well as possible development needs.
Step 2
Project KO (Kick Off Meeting)
After the ODR meeting the project manager will perform necessary project start-up procedures, define the project team and schedule a project kick off meeting. In some cases, an export license needs to be applied. An export license is granted by the Ministry of foreign Affairs or sometimes the Ministry of Defence.
Environics project team is a combination of the in-house experts from different sectors of the organization. In an early stage, typically the Project engineer, Mechanics designer and electrical designer are included in the project. Other designer / application specialists are invited to participate in case there is a customer specific R&D requirements. Procurement is also involved so that all possible long lead time equipment is added to the procurement list. Communication with other stakeholders is also initiated. After KO meeting, initial system documents are created; system wirings, cable and connector lists.
Step 3
Project Design & Execution
Usually after 1st KO meeting there are still a bunch of open questions in order to proceed with final design. It’s extremely important to have good communication with the partners and the end customer throughout the project. The next step is to have a meeting with the customer or even plan an onsite survey visit. When all questions are answered, then final design phase starts. The final design will be the confirmed in formal or informal CDR. Project documentation is also shared with the customer, so that they are able to proceed with installation planning.
Step 4
Production
After the approved CDR, customer-specific project needs are included in the manufacturing plan. Because most of our project material consists of standard off-the-shelf products, production has typically reserved a manufacturing slot for project-related material already after ODR to keep lead times as short as possible. It is a big benefit to have all main functions under the same roof, in our own hands, enabling easy communication with design team, production and procurement departments.
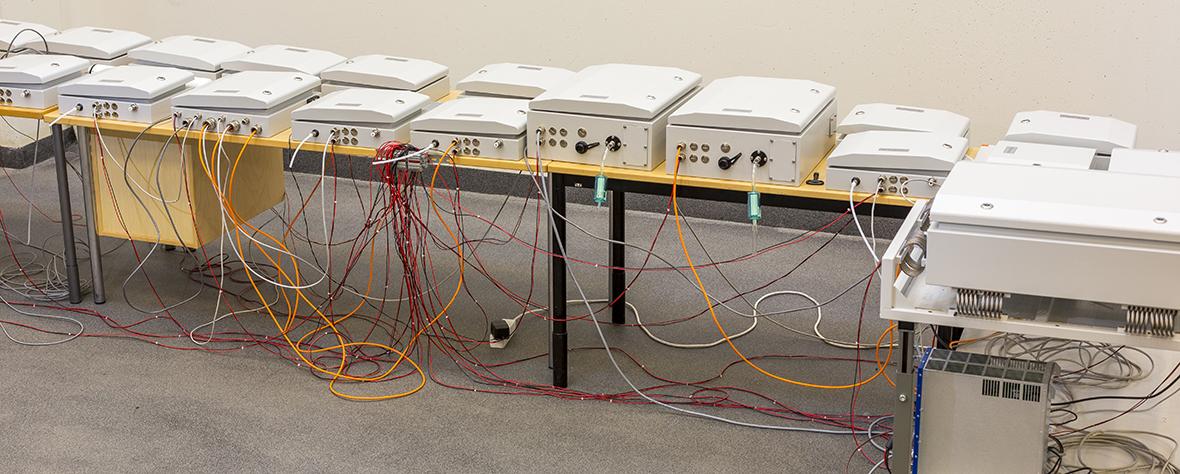
Set of standard off-the-shelf biological detectors products in Environics Oy at Environics Oy production facilities in Mikkeli, Finland.
Step 5
Testing & QA
When the production is complete, the system is installed on the test floor and quality control activities begin. At this point, the project team also includes a SW Specialist who builds all the software configurations related to the system. When all the system configurations are ready, the system functions are tested, verified and documented. In addition, if the delivery includes training, the training manager will also familiarize himself with the system so that he can prepare the training material accordingly. Once the system is complete, an internal FAT will be held. If customer FAT is included in the scope of delivery, we will agree a date and prepare a FAT agenda. We will demonstrate the working system at the FAT event. A FAT document is filled together and a copy of the FAT document is sent to the customer.

Project Manager Mikko Pöyhönen and Product Manager for CBRN Systems and Software Petri Kiukas together with an end-customer after a successful FAT (Factory Acceptance Test) at Environics Oy production facilities in Mikkeli, Finland.
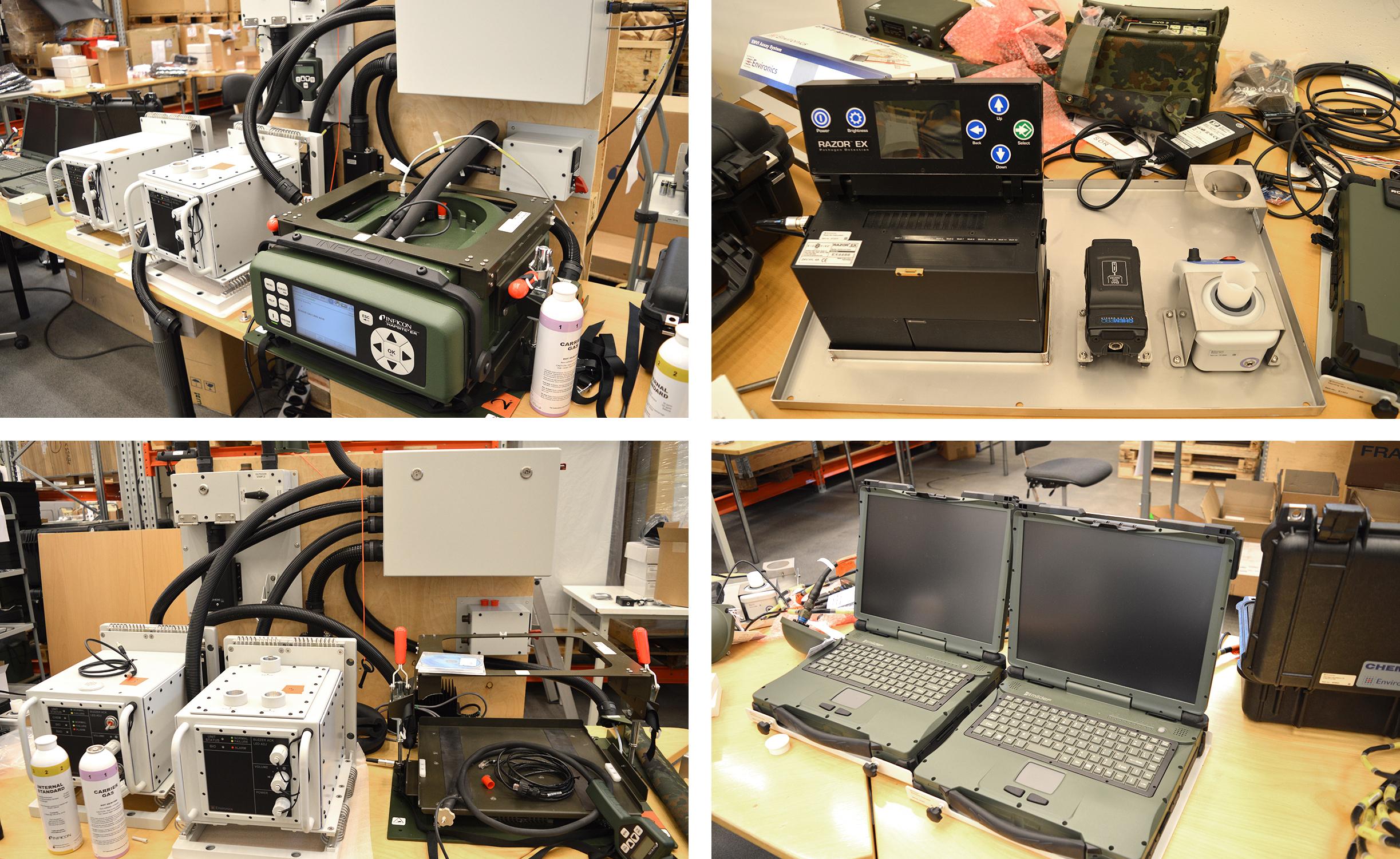
Military vehicle system functions ready to be tested, verified and documented at the test floor on Environics Oy headquarters in Mikkeli, Finland.
Step 6
Delivery
After a successful FAT the system will be packed, and depending on the delivery terms, our Logistic coordinator will proceed with shipment arrangements. CBRN equipment needs a special attention when arranging delivery; equipment containing radioactive material or lithium-ion batteries has strict transportation regulations. Fortunately, we have an extensive experience and good partners to arrange transportation system shipment almost to any airport in the world.
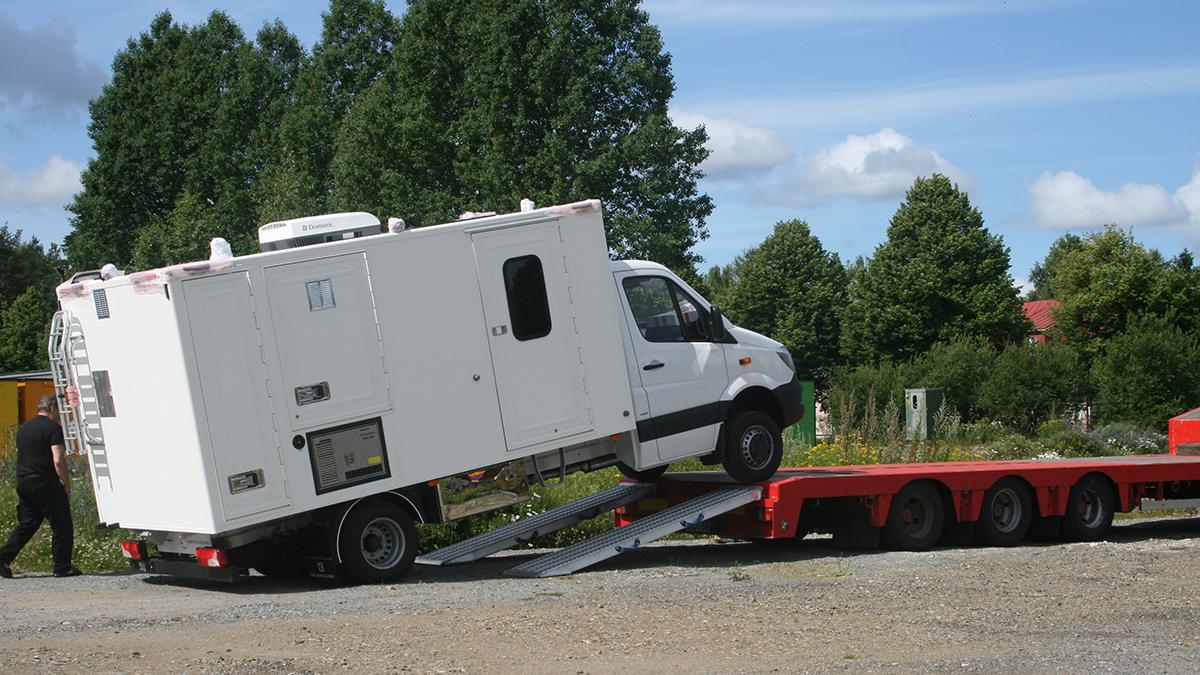
A ready light CBRN reconnaissance vehicle being shipped to the end-customer after a successful FAT conducted at Environics Oy facilities in Mikkeli, finland.
Step 7
Installation
After the system arrives to its destination, the customer is responsible for installing the system and cables according the system documentation. Installation supervision can be provided with extra cost.
Step 8
STW & Commissioning
Typical commission team: Project Engineer, SW specialist, system/ service engineer and possible training manager. After the system is mechanically installed (cables pulled etc.) our commissioning team will arrive to the site and proceed with commissioning. At commission, the system installation is checked thoroughly. After commissioning, the system is ready for use and verification test. After commissioning, our project services include usually an evaluation period when final adjustments to the system configuration will be made based on real environmental conditions.
Step 9
Training
System training can be conducted during or after the commissioning and acceptance tests, or it can be schedule for some other occasion. With proper end-user training, the customer can get the most out of his investment. Also, e-Learning courses and onsite re-fresh trainings are available to ensure the capabilities exist even if the crew/staff is changing.
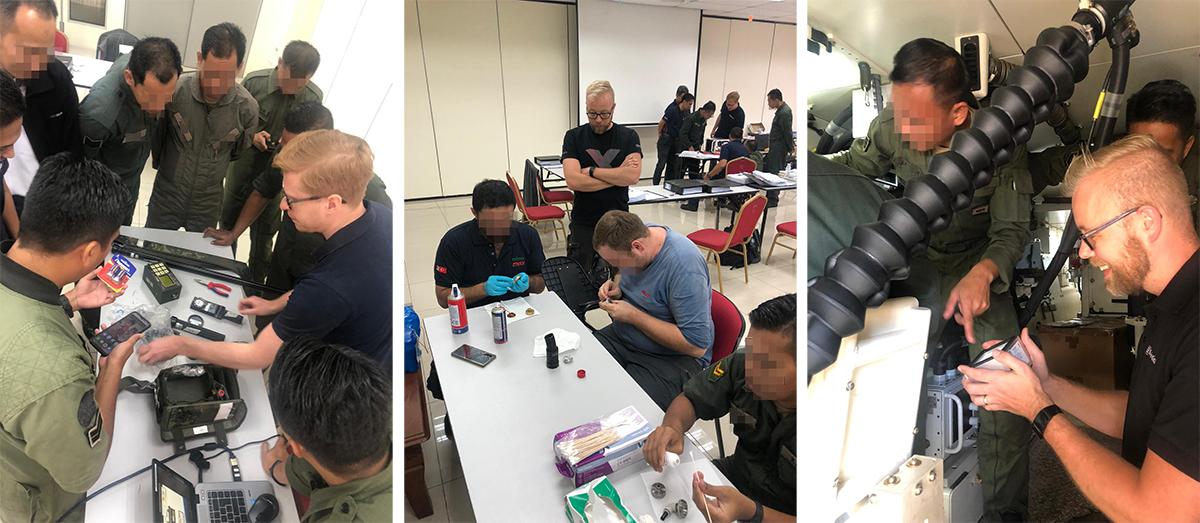
Training Manager Toni Leikas and Service Engineer Niko Räsänen conducting an onsite end-user training after the project delivery.
Step 10
SAT/HAT
Project commissioning team will conduct SAT/HAT together with the customer, in order to verify and document the system performance and functions. After the acceptance test, the system documents are updated (if needed).
Step 11
Project Closure
After a successful acceptance test, the system warranty period starts. When all project related tasks are completed, the Service team will take the ownership. The project is completed and can be closed. Even though the project is finalized, a close communication and relationship with the customer continues through the lifespan of the system and beyond.
Leave a Reply